Electronics are distributed everywhere. However, there are countless environments wholly unfriendly to circuit boards. Electronic equipment needs specialized protection to be able to work through adversity and deliver the technological promises they make. One of the standards for industrial protection of electronics is conformal coating. This coating provides a layer of defense that protects against high temperatures, moisture, corrosive chemicals, and even electric shocks. For example, salt fog from coastal regions, exhaust fumes from traffic, particulates from factory operations, and airborne chemicals from refineries are locations where industrial equipment, such as Ethernet switches, will need extra protection to operate.
Learning about conformal coating can help you pick devices and components that are verifiably up to the challenges that will face them. This post covers the essence of the most common conformal coatings and their uses.
What Is Conformal Coating?
The most basic answer is that a conformal coating is a protective membrane applied to printed circuit boards. More specifically, it is a coating that, through various application processes, molds to precisely fit the contours and structure of differing topologies — hence the name. The material conforms to the object they are protecting, rather than looking to a one-size-fits-all method of sheathing or shielding.
There are a large number of materials and application methods used to work conformal coatings onto electronics. Each comes with different advantages and disadvantages, and each of the conventional conformal coatings shines in different environmental settings. In general, a conformal coating prevents moisture from corrupting a circuit while allowing internal moisture to leave the environment. The other protective elements will vary by the coating used.
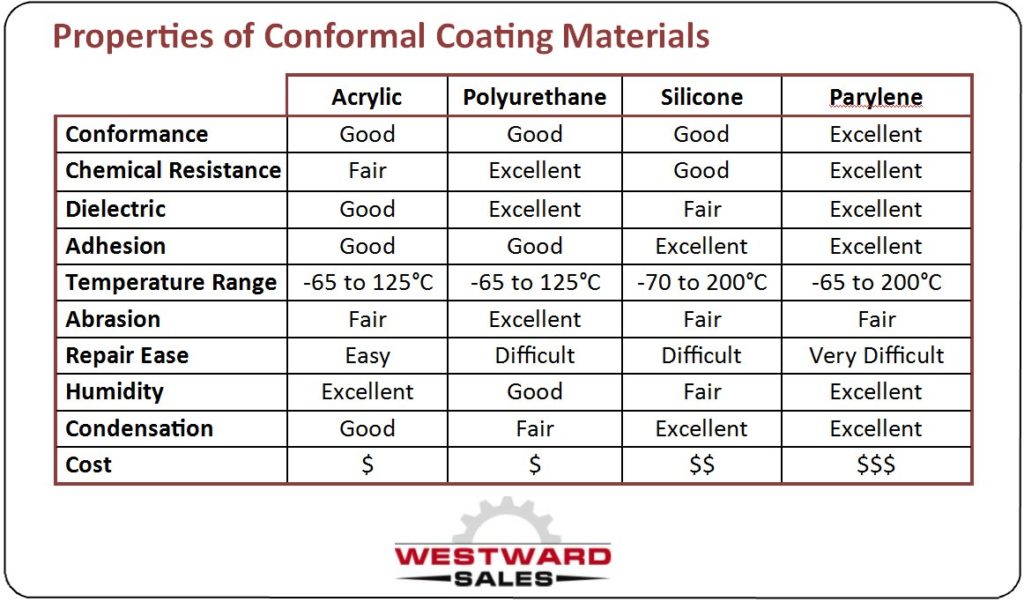
Acrylic Conformal Coating
Acrylic resin, a type of thermoplastic, is derived from acrylic or methacrylic acid, lending to the name. It yields a polymer with a crosslinked structure. Acrylic resin is commonly used in latex-based paints to give them better resistance against peeling, cracking, blistering, and other adverse effects.
In conformal coating, acrylic resin is known as the all-around coating. With relatively thin membranes, it provides robust protection against humidity, temperature variations, and ingress. It’s particularly noted for hydrolysis resistance (which prevents water-based corrosion of electronic components), clarity, and low darkening.
The most notable distinction of acrylic resin is its susceptibility to chemical solvents. This is seen as a strength and weakness. Acrylic coatings are easy to remove without abrasion, making them highly reworkable, but they are a poor choice for operations that will expose circuit boards to chemical solvents. When it comes to chemical protection in general, they get the lowest score.
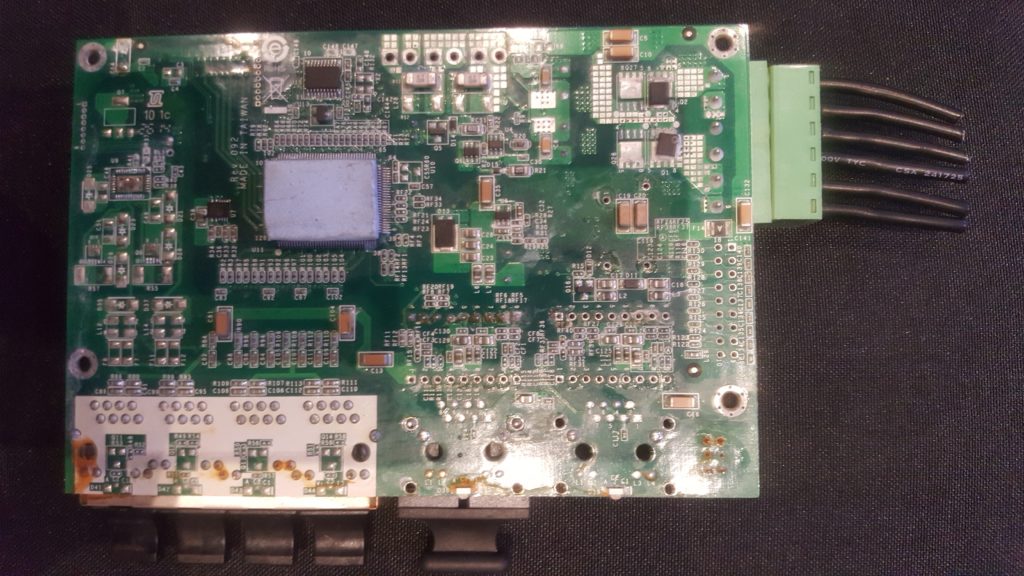
Polyurethane Conformal Coating
Polyurethane is typically not a thermoplastic, although it can be. It is created by joining carbamate (or urethane) links. This technique creates thermosetting polymers called such because they do not melt even in high heat. Polyurethane is highly adaptable and used in applications from seals and adhesives to coating synthetic fibers.
When it comes to conformal coatings, polyurethane resin is coveted for its moisture and chemical resistance. It is difficult to find a solvent that can penetrate a polyurethane barrier, and this makes it a top candidate for chemical processing applications and environments with a wide range of corrosive elements.
Among chemically resistant coatings, polyurethane resin is one of the most resistant to abrasion. It is one of the most durable substances, but also the most difficult to rework. In the very harshest environments, polyurethane is a popular choice. In settings where boards need frequent or semi-frequent redeployment, polyurethane is one of the worst options possible.
Silicone Conformal Coating
Silicone resins are developed by branching oligosiloxanes. They can be built from many chemical structures, and each choice yields different valuable properties for the final result. In most cases, silicone resins are ingredients in thermoset polymer matrix composites. And, this is the case when used for conformal coatings.
Silicone resin has three notable strengths. It is very flexible, making it ideal for vibration resistance. It is exceptionally resistant to heat changes and is one of the best thermal insulators available for electronic components. It is also very chemical resistant. Applications that involve heavy moisture, salt spray, and a wide range of chemical solvents will benefit from silicone coatings.
The glaring weakness of silicone is its softness. The resin is susceptible to abrasion. Locations where the coating will be subjected to abrasion are a non-starter. For silicone resins deployed in high wind regions, an additional layer of ingress protection is necessary.
Parylene Conformal Coating
Parylene is substantially different from the coatings discussed so far. Everything until now has been a specialized polymer fabricated for the desired application. Parlyene refers to the method of developing the polymer more than the end-state chemical itself. Essentially, parylene uses chemical vapor deposits to make polymer barriers. It is an extremely specialized technique, and only vapor phase deposition equipment may apply a parylene barrier to a circuit board (or any other object).
This process makes parylene coatings more expensive on average than other options. A high price comes with some important perks, however. Parylene is explicitly designed for its high dielectric strength and moisture resistance. It’s the best of the best for electrical insulation. Because parylene is still polymer-based, it provides excellent protection against solvents and extreme temperatures. In many applications, it offers some of the highest protection available for a conformal coating. If the cost is justifiable, it’s often the champion of defense.
Aside from the cost, there is another downside to parylene membranes. They are among the most difficult to remove. Combine that with the specialized equipment needed to apply a new parylene coating, and you have the conformal coating that is the very worst for reuse. Parylene is best for components that are meant to be installed and stay there.
Available Conformal Coated Devices
There are qualified shops that conformal coat electronic circuit boards. However, a large minimum order and lengthy lead-time are usually required. Fortunately, some devices are conformally coated during the manufacturing process and are available in large or small quantities. Products like the LNX-800A-T-CC from Antaira Technologies are in stock and ready to ship. When considering this Ethernet switch and other pre-coated switches like it, compare the labels to see which process was used and select the proper coating for your working environment. The right choice will enhance the reliability and working life of your communication infrastructure.
Leave a Reply